theBaron
Major
- Joined
- Mar 27, 2008
- Messages
- 10,437
Hi, all! This afternoon, I fired up the forge and broke out some molds, to cast some figures. I thought I would take some pictures during the process and post them here, to help illustrate what we've so often talked about.
The first picture is a shot of my melting pot:
The pot I use is made by Hilts Molds of Nevada, and they call it "The Hot One" I bought it years ago at a sporting goods store, that sold black-powder supplies. This holds a couple of pounds of metal, and melts it via a heating coil in the bowl of the ladle. It came with a stand made of a piece of stamped sheet steel, which I bolted to a piece of plywood as a base.
The large metal square is a homemade casting plate, which is intended to protect any surface beneath it, and to contain any metal that might happen to flow where it's not supposed to.
I cast in my garage, and I have the rig set up on an old Workmate, set up in the doorway, for good ventilation.
Here is a shot of some of my metal molds:
These are modern copies of the old bronze molds from Germany, from the firm Schneider Bros. They make half-round figures. These newer molds are not as good as the original German molds. But that's not unexpected, since these American copies are actually derived from the original German castings, copied here in the 30's by the Rappaport Brothers (Junior Caster).
Here are some more of my metal molds:
These are also copies of the old Schneider molds, but they were made in Germany by a gentleman named Höhmann, who made his molds from the original Schneider masters. These are of a zinc alloy, and produce very crisp castings.
Next, this is a tool that I've mentioned in some of our threads about casting:
That is an aluminum muffin-top pan. I use it to make casting pigs out of my metal supply. The pigs are about the size of a silver dollar, and are in much more convenient form than the bars of metal that I have.
Speaking of metal, here is a shot of some of my casting metal:
The bar in the center is the last remnant of a 25-lb bar of linotype metal that I bought from a fellow who cleans out old print shops. It was originally about 28 inches long (sorry, metric people, you'll have to do your own math!) and very unwieldy. That's what inspired me to process it down into casting pigs.
Some more metal, this time, a supply of lead:
Those are tire weights. I add those to the linotype alloy, depending on the mold. My metal molds like linotype, which is high in tin content, with some antimony, but that alloy is a littler hotter than an alloy with a little more lead in it, which I use for some of my rubber molds.
Speaking of the rubber molds, here is a typical one, a mold of a Prussian cuirasser:
Once I fired up the pot, the first thing I did was to finish rendering the bar into the smaller pigs:
and here is a shot of some finished pigs:
Those go in the can, and we're ready to break out some molds.
Casting follows in the next post....
The first picture is a shot of my melting pot:
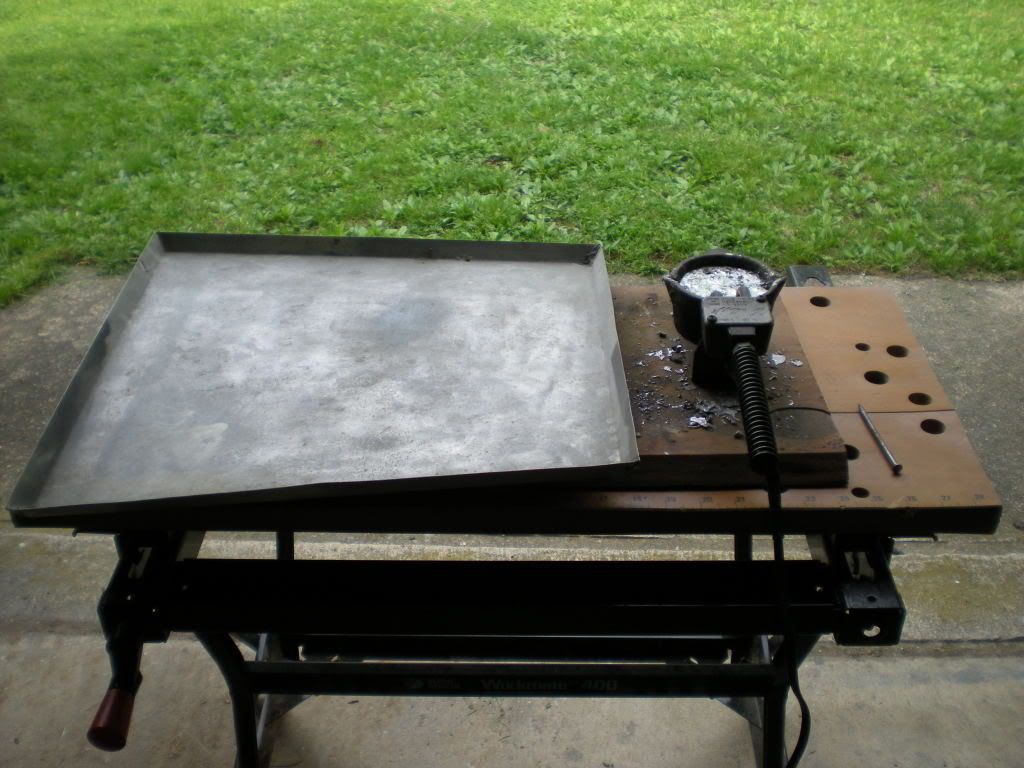
The pot I use is made by Hilts Molds of Nevada, and they call it "The Hot One" I bought it years ago at a sporting goods store, that sold black-powder supplies. This holds a couple of pounds of metal, and melts it via a heating coil in the bowl of the ladle. It came with a stand made of a piece of stamped sheet steel, which I bolted to a piece of plywood as a base.
The large metal square is a homemade casting plate, which is intended to protect any surface beneath it, and to contain any metal that might happen to flow where it's not supposed to.
I cast in my garage, and I have the rig set up on an old Workmate, set up in the doorway, for good ventilation.
Here is a shot of some of my metal molds:
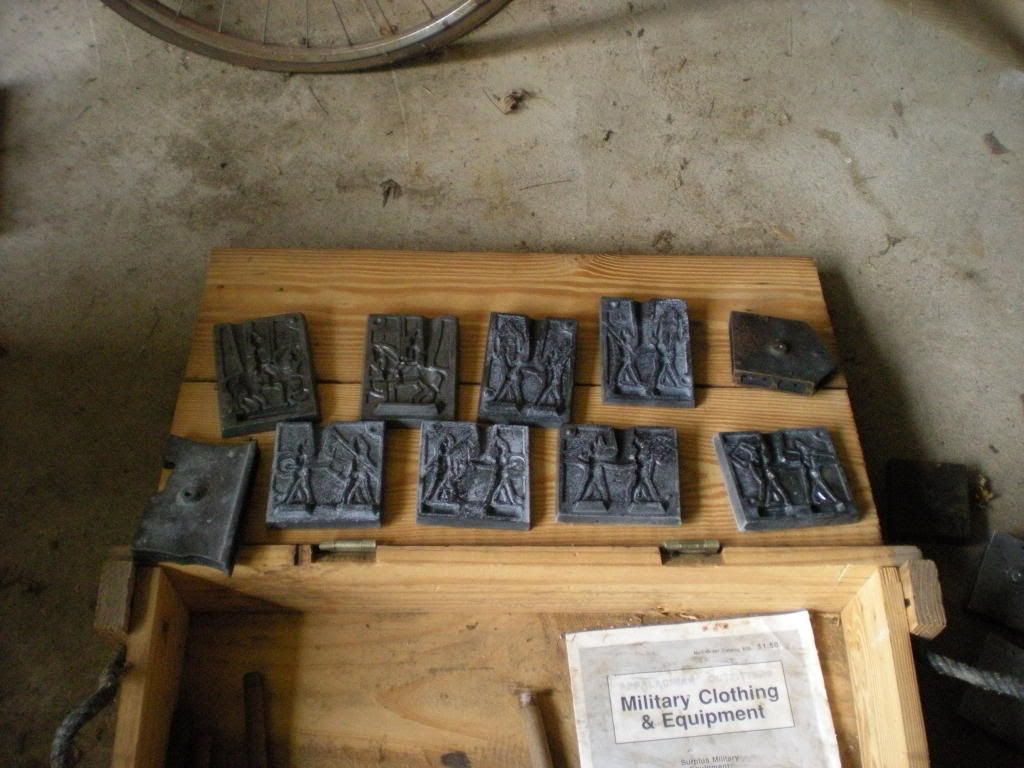
These are modern copies of the old bronze molds from Germany, from the firm Schneider Bros. They make half-round figures. These newer molds are not as good as the original German molds. But that's not unexpected, since these American copies are actually derived from the original German castings, copied here in the 30's by the Rappaport Brothers (Junior Caster).
Here are some more of my metal molds:
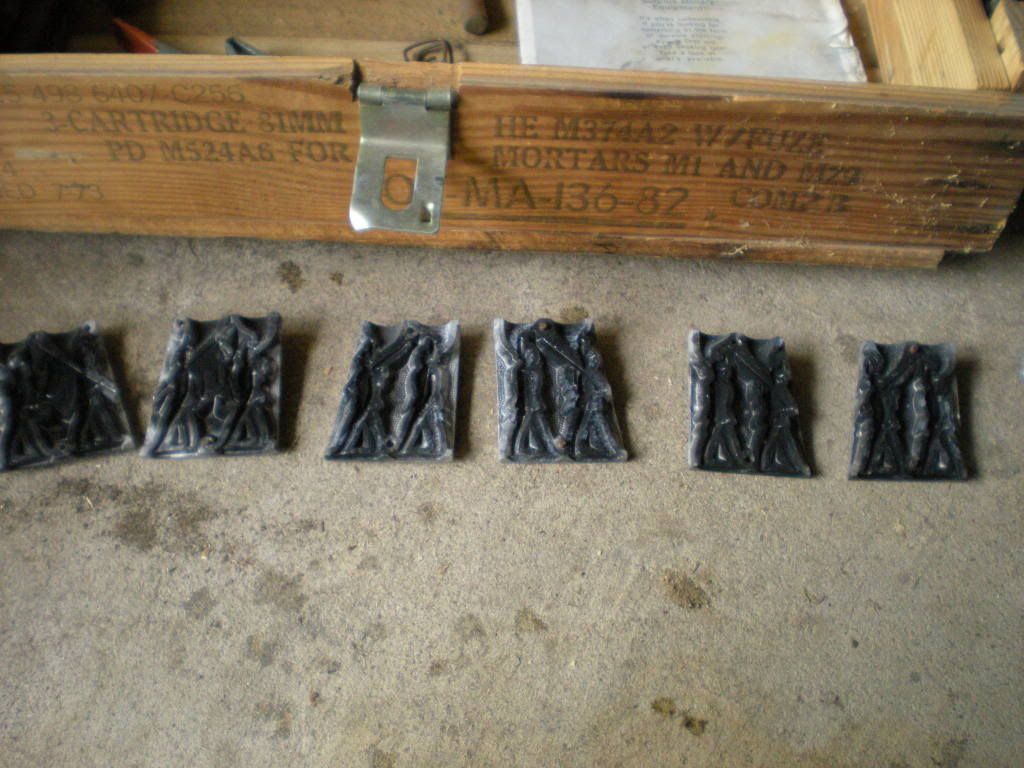
These are also copies of the old Schneider molds, but they were made in Germany by a gentleman named Höhmann, who made his molds from the original Schneider masters. These are of a zinc alloy, and produce very crisp castings.
Next, this is a tool that I've mentioned in some of our threads about casting:
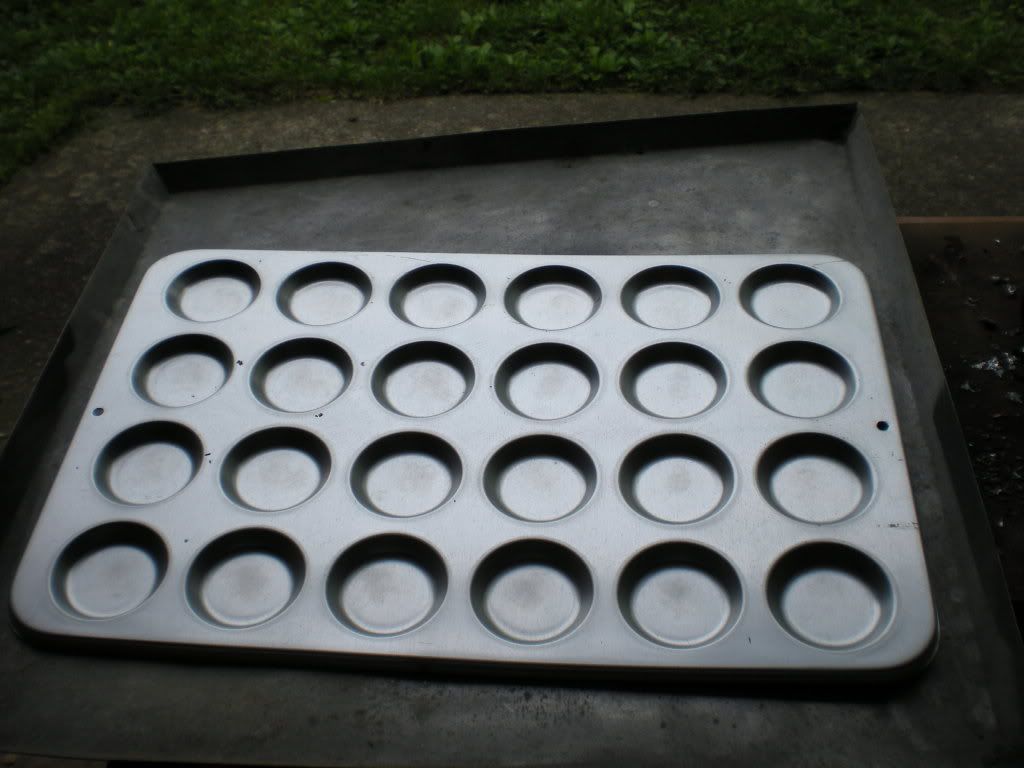
That is an aluminum muffin-top pan. I use it to make casting pigs out of my metal supply. The pigs are about the size of a silver dollar, and are in much more convenient form than the bars of metal that I have.
Speaking of metal, here is a shot of some of my casting metal:
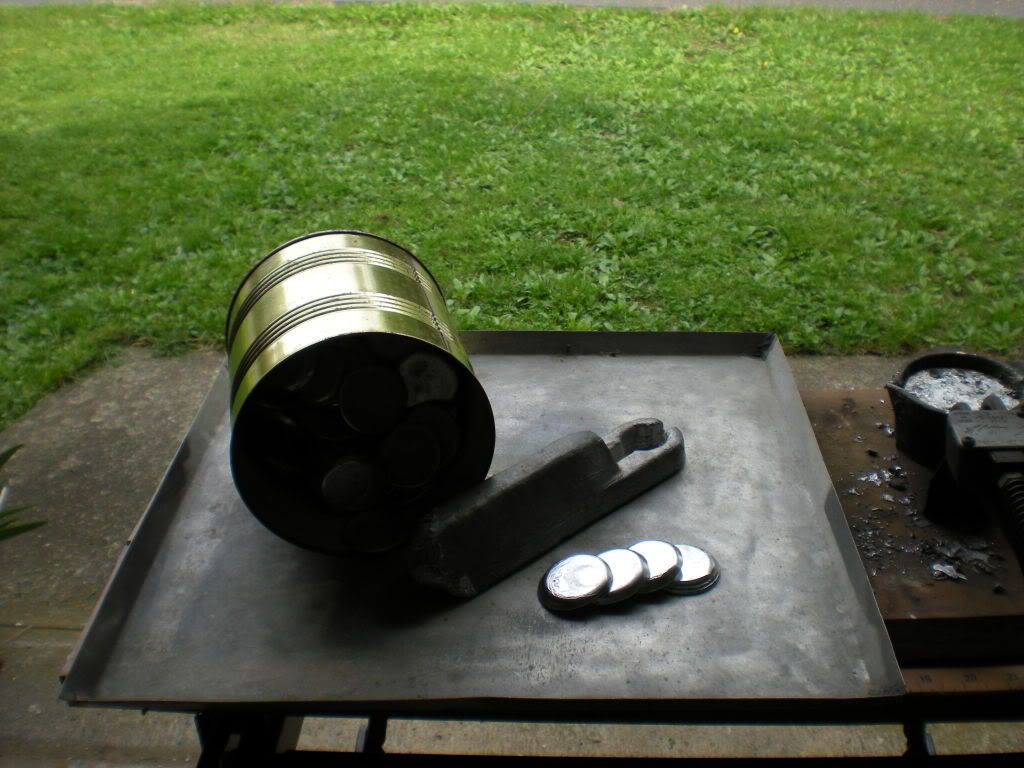
The bar in the center is the last remnant of a 25-lb bar of linotype metal that I bought from a fellow who cleans out old print shops. It was originally about 28 inches long (sorry, metric people, you'll have to do your own math!) and very unwieldy. That's what inspired me to process it down into casting pigs.
Some more metal, this time, a supply of lead:
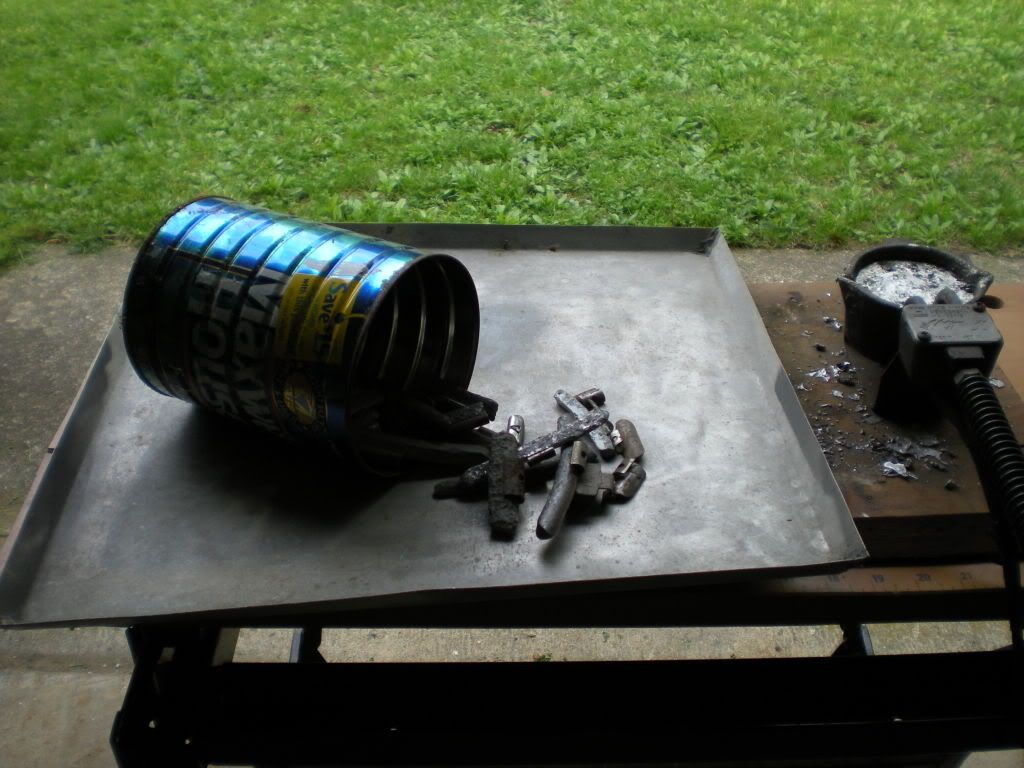
Those are tire weights. I add those to the linotype alloy, depending on the mold. My metal molds like linotype, which is high in tin content, with some antimony, but that alloy is a littler hotter than an alloy with a little more lead in it, which I use for some of my rubber molds.
Speaking of the rubber molds, here is a typical one, a mold of a Prussian cuirasser:
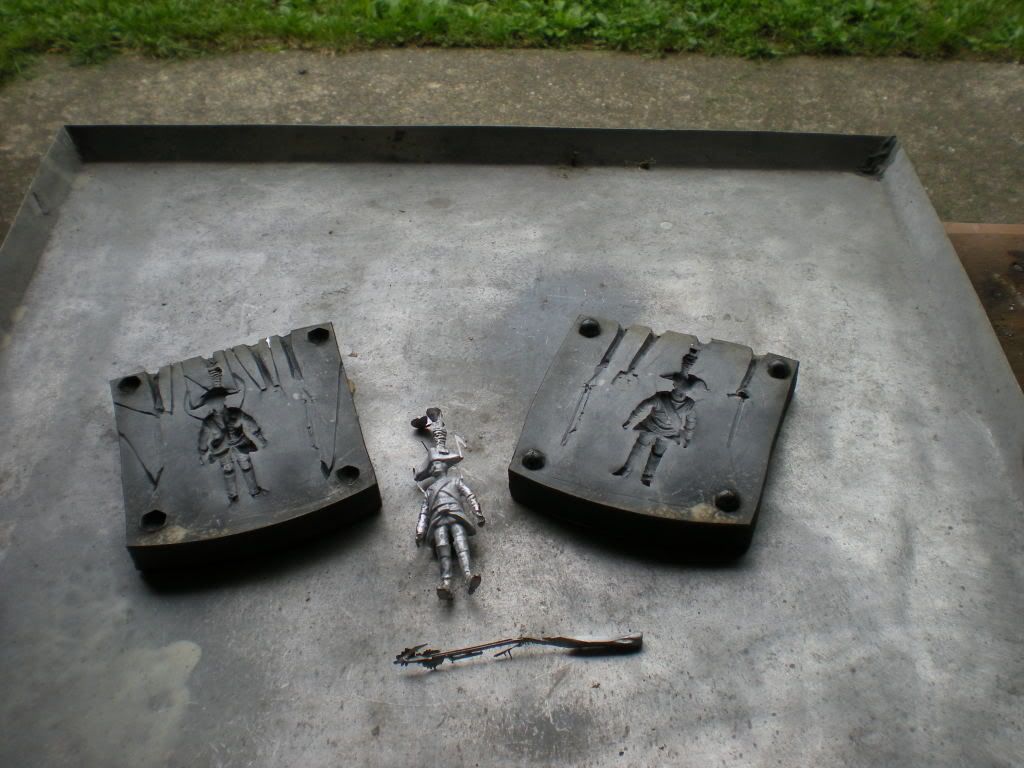
Once I fired up the pot, the first thing I did was to finish rendering the bar into the smaller pigs:
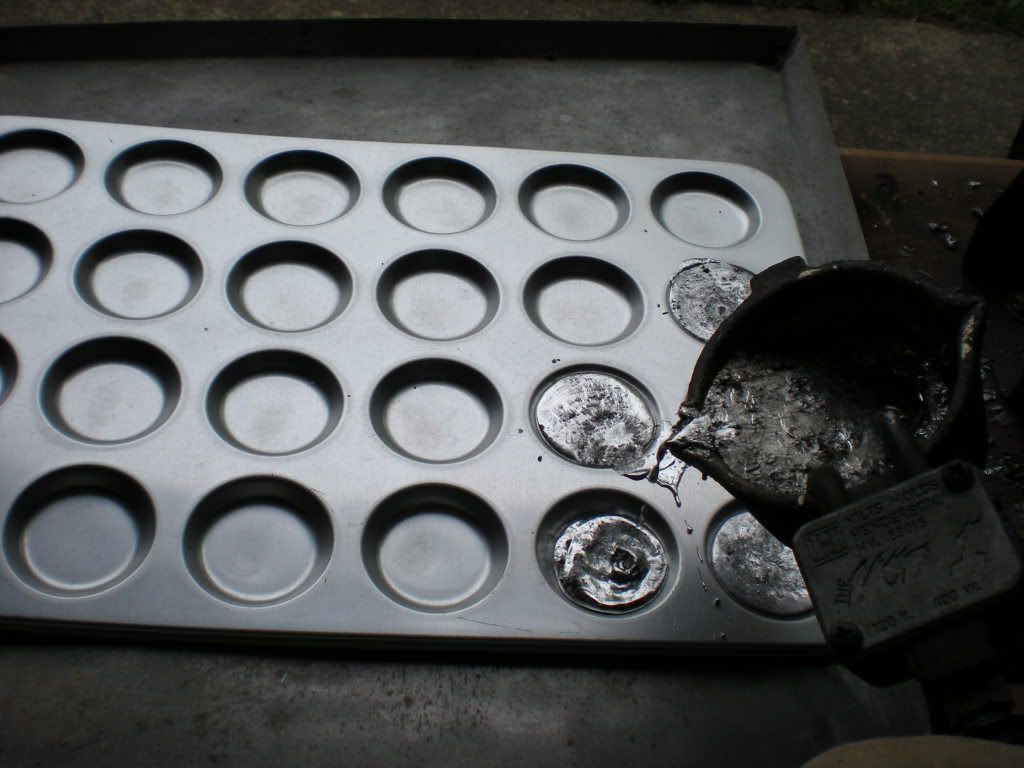
and here is a shot of some finished pigs:
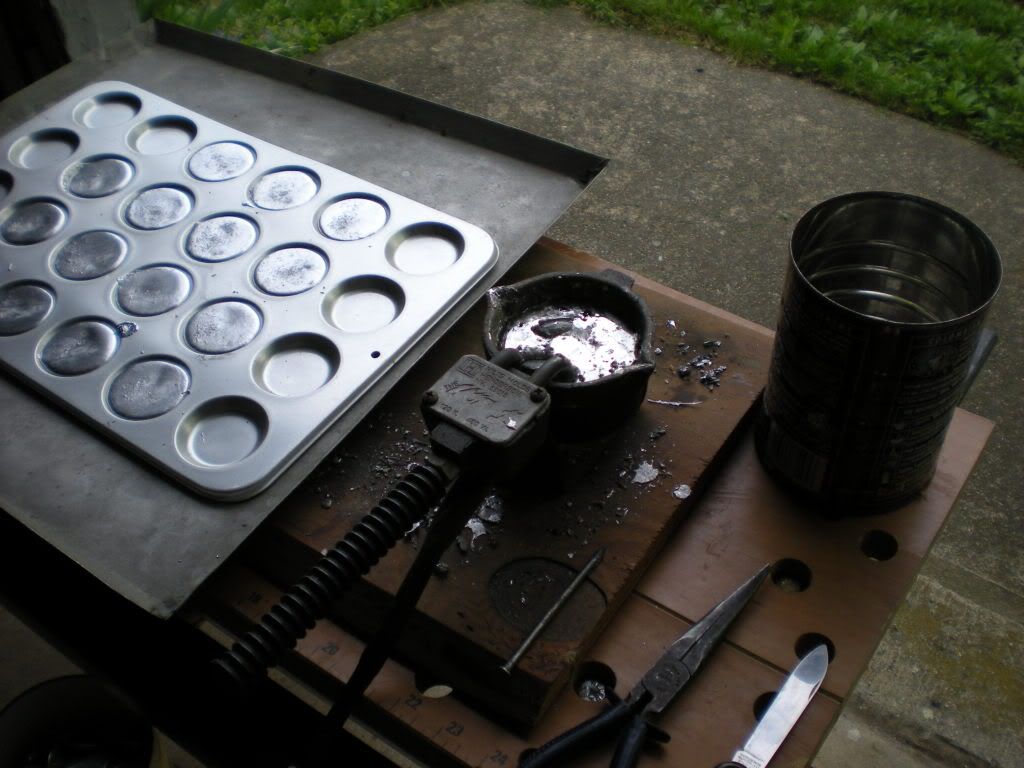
Those go in the can, and we're ready to break out some molds.
Casting follows in the next post....