Wolfgang_UK
Sergeant
- Joined
- Dec 5, 2009
- Messages
- 695
Hi,
I did a bid of resin casting lately which some of you might find interesting.
All figures are 70mm scale either sculpted by myself or altered by pure magic (see pictures).
Silicone rubber (the light green stuff) used is a great knew product I have found recently
made by a company called PUREX it is called PICOSIL-GRUEN, mixes 1:1 by volume
and sets in about 30 minutes - fantastic stuff. It is supposed to work with low melt
whitemetals as well but I could not test it yet. Vulcanised molds last for at least 50 castings in resin which is absolutley premium since the usual rate 15-20 castings. Mind you all my castings are one piece castings which does put a lot of stress to the molds due to the "Pulling-Forces" involved.
Resin used was EazyFlow 60. Both rubber and resin was cured under ca. 90 PSI pressure resulting in absolutly bubble free molds and castings.
Enjoy
regards
Wolfgang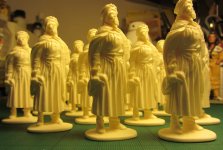
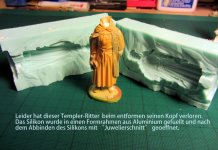
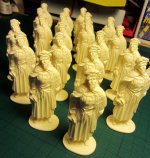
I did a bid of resin casting lately which some of you might find interesting.
All figures are 70mm scale either sculpted by myself or altered by pure magic (see pictures).
Silicone rubber (the light green stuff) used is a great knew product I have found recently
made by a company called PUREX it is called PICOSIL-GRUEN, mixes 1:1 by volume
and sets in about 30 minutes - fantastic stuff. It is supposed to work with low melt
whitemetals as well but I could not test it yet. Vulcanised molds last for at least 50 castings in resin which is absolutley premium since the usual rate 15-20 castings. Mind you all my castings are one piece castings which does put a lot of stress to the molds due to the "Pulling-Forces" involved.
Resin used was EazyFlow 60. Both rubber and resin was cured under ca. 90 PSI pressure resulting in absolutly bubble free molds and castings.
Enjoy
regards
Wolfgang
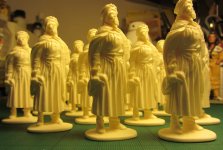
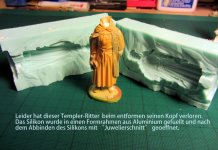
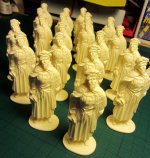