fishead19690
Command Sergeant Major
- Joined
- Nov 3, 2005
- Messages
- 2,555
I was messing around with some green stuff and scratch built this dead Prussian hussar. The scale is somewhere between 54mm and 60mm? About the size of a Britians figure. It was fun to make, I might try a few more?
I,m no sculptor but with more practice they might get better????? I don,t have enough patience to let the putty fully dry before moving onto the next section and I ruined a lot of the detail I had better the first time around.
I had the hands and feet better before I destroyed them and had to glue one of the hands back on.
Hopefully the next try will go better?
I,m no sculptor but with more practice they might get better????? I don,t have enough patience to let the putty fully dry before moving onto the next section and I ruined a lot of the detail I had better the first time around.
I had the hands and feet better before I destroyed them and had to glue one of the hands back on.
Hopefully the next try will go better?
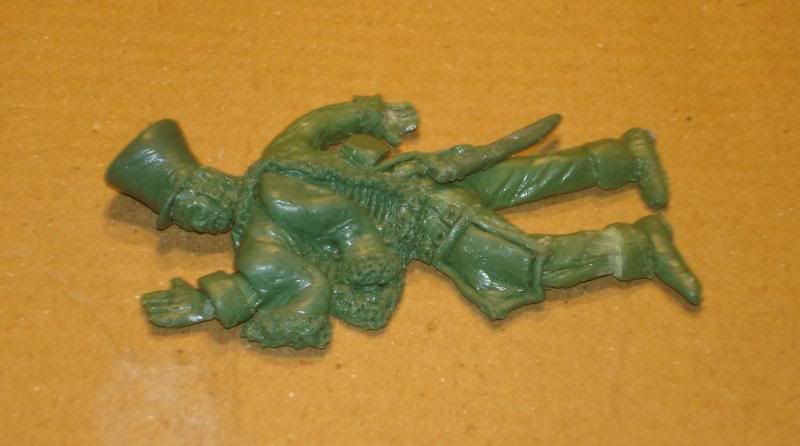
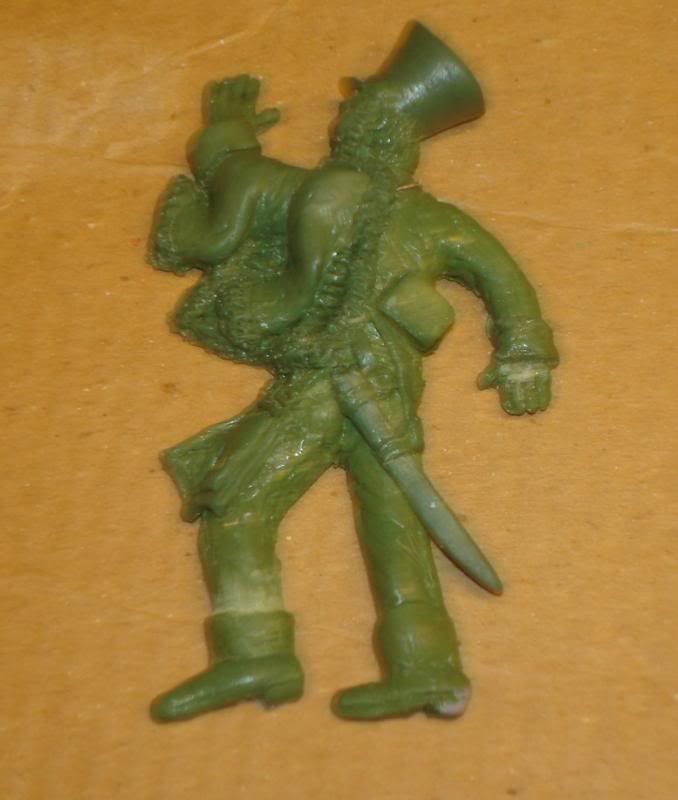
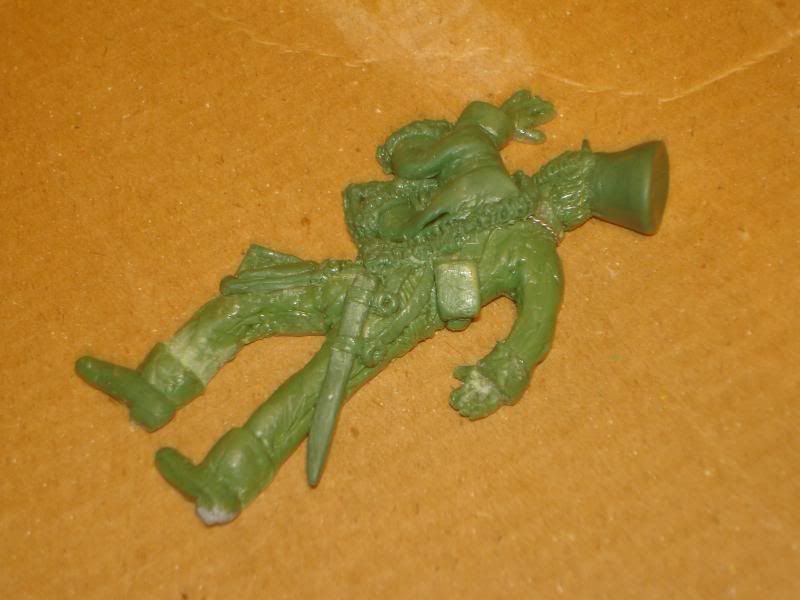
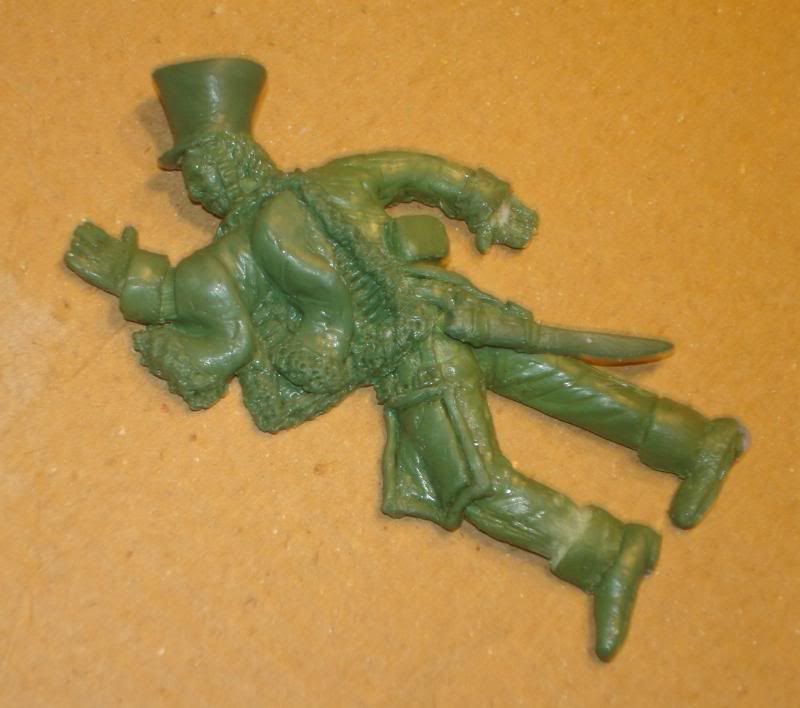